What are the three building blocks of lidar technology?
The basic functionality of lidar technology can be understood through three building blocks: transmission, detection, and imaging.
Transmission refers to the emission of lasers (infrared or near-infrared light) from a lidar sensor. When you hear someone talk about 850nm, 905nm or 1550nm lidar, they are in fact labeling the lidar by its transmission technology. The choice of transmission technology is closely associated with the wavelength of the laser used.
Detection occurs when the lidar receives returned signals. Time of Flight (ToF) is the most common operational principle for distance measurement. Some lidars use Frequency Modulated Continuous Wave (FMCW). We will explain further later in this blog post.
Imaging is the process by which the lidar transforms detected data points into a point cloud, a 3D representation of objects within a specified field of view. You may have come across terms like “solid state”, “MEMS”, and “flash lidar”; these are all different imaging mechanisms.
Transmission, detection and imaging are highly interrelated modalities of lidar design. Different wavelength choices are paired with different detection methods and imaging mechanisms. Our CEO, Dr. Jun Pei, provides a more detailed explanation in this Forbes article.
Simply put, Cepton currently uses 905nm laser combined with ToF and our patented imaging technologies (MMT® and its next-gen innovation). This combination was optimized for mass-market lidar adoption, utilizing mature, OEM-validated building blocks.
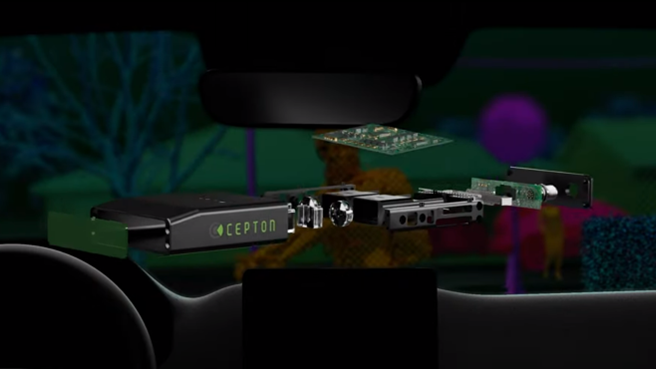
What advancements have been made in beam steering technologies to increase lidar’s scalability?
Beam steering technology, or imaging technology, plays a crucial role in the performance and usability of lidar systems. It determines how light is steered within the architecture to scan an environment to collect 3D data. The goal is to generate a dense 3D point cloud within a short period of time, across a wide field of view.
Rotational lidars were one of the firsts used for autonomous driving and other smart applications. One of their biggest challenges is integration – a spinning pod on the rooftop is fundamentally incompatible with a sleek vehicle design. They have also become less preferred due to low efficiency high complexity, high cost and low reliability. Flash lidars have been widely used in many devices, including iPhones. But when it comes to mass-market adoption for automotive use, they suffer from poor range, high power consumption and limited field of view. MEMS (Micro-Electro-Mechanical Systems) lidars were designed to reduce size, power consumption and mechanical wear from moving parts. However, the use of micro mirrors introduces low durability, complexity with calibration, sensitivity to vibration and shock and low manufacturability. Optical Phase Array is another solid-state beam steering technology. It makes the lidar compact, easy to integrate and free from mechanical wear, but has not been a scalable solution to automotive lidar due to complexity with calibration and data processing, high manufacturing cost and low stability across different environments.
Cepton was founded in 2016 to focus on innovation in lidar imaging technology that specifically addresses scalability issues. Our first-generation imaging technology MMT® (Micro Motion Technology), a mirrorless, frictionless and rotational-free architecture, was one of the first lidar technologies truly validated by global automotive OEMs.
Building on our unique experience industrializing MMT lidar, we made yet another lead in lidar innovation. Our newly introduced Ultra lidar uses Cepton’s next-generation imaging technology, MagnoSteer™. MagnoSteer extends MMT’s key strengths in achieving an optimal balance between performance, reliability and cost, but uses an even more streamlined architecture to further increase system and software efficiency.
MagnoSteer changes the game by eliminating the compromise between efficiency and form factor. It minimizes the time, space and energy wasted within the architecture as it generates extremely dense point clouds, resulting in impressive data rate from an extremely small package. Its new scan pattern further simplified calibration and data processing. As a result, MagnoSteer enables significantly improved performance, including 50% longer range and ultra-high resolution, while minimizing size, power consumption and manufacturing cost.
The invention of MagnoSteer was driven by real OEM needs, offering a frictionless, automotive-grade solution with an infinite mechanical life. It consumes less than half the power of typical scanning systems that deliver comparable performance, while taking up as little as one-fourth of the space.

Is 1550nm lidar better than 905nm lidar?
A lidar’s wavelength choice largely depends on specific application requirements.
1550nm lidar typically offers longer range due to reduced laser beam size and higher tolerance of power for eye-safety. This makes 1550nm lidars ideal for long-range applications with high tolerance for power consumption and cost, such as military and defense, research and space exploration.
However, in automotive applications, the story is different. While “seeing” past 300m is never a drawback, assisted and automated driving capabilities under current speed limits don’t require excessively long range. With proper design and advanced signal processing, 905nm lidars can easily achieve the required 200m to 250m range while consuming just a fraction of the power. For vehicle integration, a lidar’s power efficiency might be more important than you think – we’ll explain here.
It's also important to note that lidar eye safety isn’t solely determined by wavelength - in fact, 1550nm lasers are widely used in medical procedures. Eye safety depends on many other factors including laser power, exposure time and repetition rate. To learn more on the topic, check out this post.
1550nm light is considered safer for the eye as it’s absorbed by the cornea to a greater extent than 905nm light before reaching the retina. That means 1550nm lasers have a higher eye-safe power threshold, which, as explained above, isn’t helpful for automotive adoption. In automotive lidars, 905nm light is used well below the eye-safe power threshold, maximizing the power efficiency of the entire sensor.
Finally, while 905nm lidars rely on mature laser technology, using primarily cost-effective semiconductor materials, 1550nm lidars use optical fibers that are more expensive and more difficult to manufacture in volume.
We are yet to see which wavelength will dominate the future of lidar technology. However, to make lidar usable in today’s vehicles, we believe benefiting from the reliability and cost-effectiveness of the 905nm laser is the right path to take.
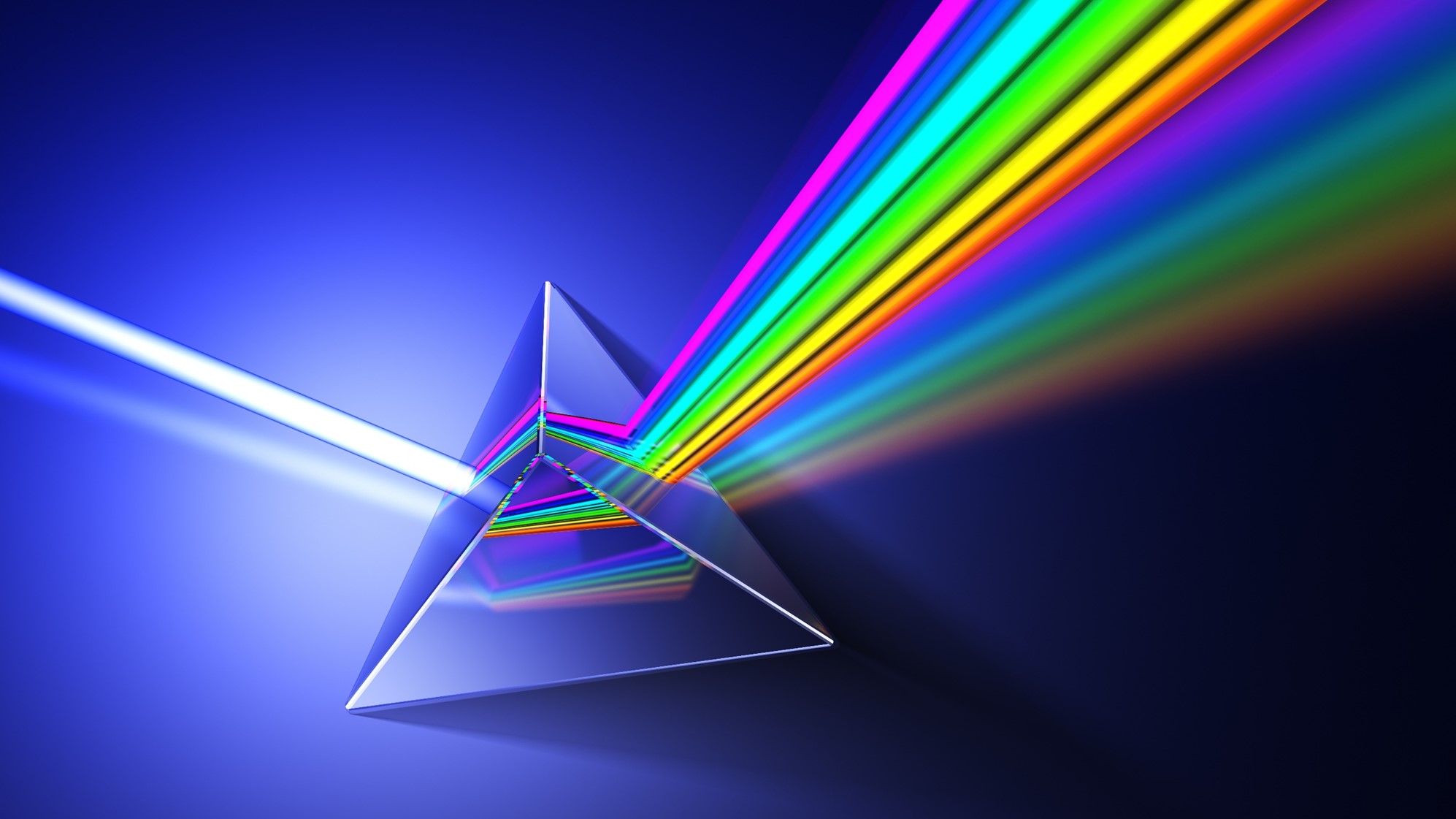
What’s the difference between ToF and FMCW?
In lidar design, Time-of-Flight (ToF) and Frequency Modulated Continuous Wave (FMCW) are two common operational principles used for distance measurement.
ToF measures the time it takes for a laser pulse to travel from the lidar device to an object and back to the sensor. As the speed of light is constant, the lidar uses ToF to calculate its distance to the obj
FMCW lidar emits a continuous wave laser with a varying wavelength. When the laser beam reflects off an object and returns to the lidar, the wavelength variation translates into a frequency shift that is used to calculate the distance to the object.
FMCW is praised as a more sophisticated detection method due to its ambient light immunity, high range resolution and motion sensitivity. However, it requires more complex signal processing techniques, which creates challenges for data acquisition, system efficiency, power efficiency and affordability. At the same time, the laser sources used for FMCW detection need to offer higher wavelength precision, placing stringent requirements on supply.
ToF offers the maturity and simplicity that are indispensable to lidar’s mass-market adoption. Compared to FMCW lidars, ToF lidars boast more streamlined hardware design, easier calibration, wider field of view, lower power consumption and higher volume manufacturability. Advanced signal processing ASICs help ToF lidars achieve an optimized signal-to-noise ratio to maximize performance and accuracy while being highly reliable, energy-efficient and cost-effective.
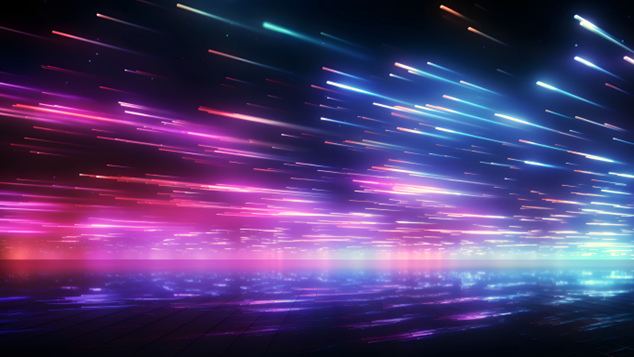