Recently, my company Cepton announced an agreement for a $100 million investment from Koito Manufacturing, a leading automotive lighting tier 1 supplier and Cepton’s longtime technology and manufacturing partner. This marks Koito’s third investment in Cepton as well as a new chapter of our history of collaboration since 2017.
When I was signing the investment agreement, I was taken back, for a moment, to my trip to Koito a few months ago, where I witnessed first-hand another example of how Japanese craftsmanship plays a key role in ensuring top-quality production of automotive products.
To cast our minds back, Cepton and Koito together secured a significant ADAS lidar series production award from General Motors in 2019. When that happened, I was invited by Koito’s top management to pay them a visit in Japan, but the pandemic had been holding me back until this past summer.
When I finally took my trip to Koito, I got to visit one of their facilities, where Cepton lidars were being manufactured to prepare for the series production in our joint flagship lidar program. More than two years after the deal was secured, Cepton and Koito had already made tremendous progress in the execution of the program. Although I had learned some stats about the milestones we had achieved, seeing it for myself was a completely different experience.
I stood there watching our products roll off the production line, unit after unit, and I felt extremely proud of how far we’d gone in our joint journey. I was ready to spend another hour just standing there, enjoying the moment, when everything stopped, and a red light flashed onto a unit, signaling the detection of something wrong.
My heart sank a little. I was eager to find out what it was.
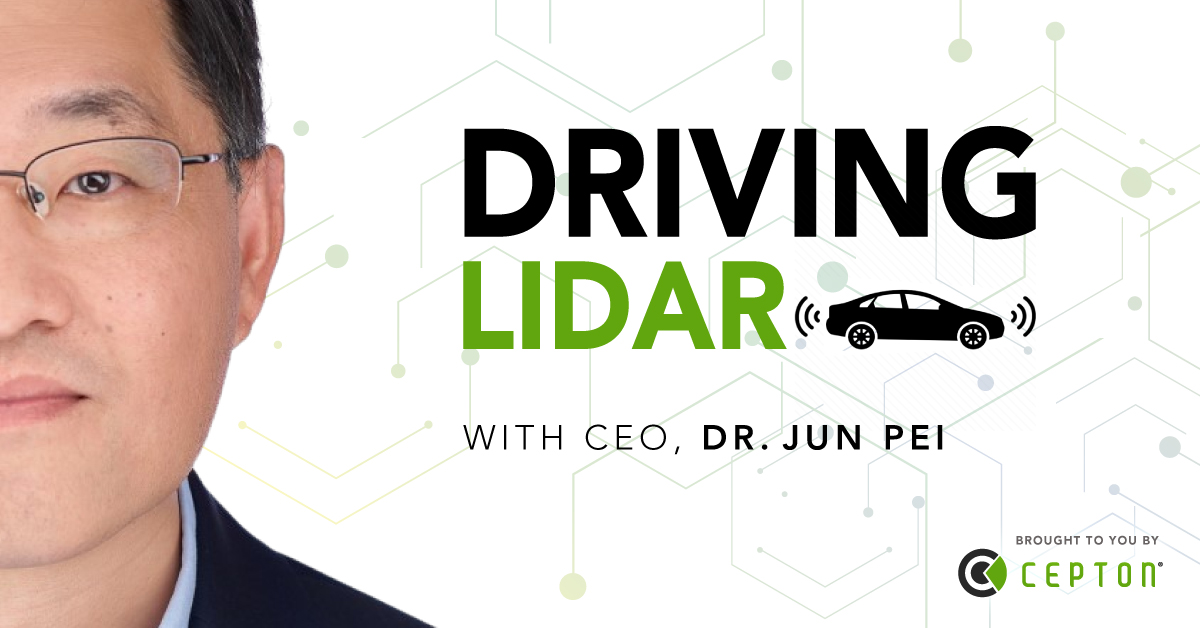
After careful examination, I was told that a letter on the label at the back of the “problematic” sensor was a little bit smudged.
That was it? I probably jumped a little, trying my best not to cry out loud.
Note that when the lidar sensor is integrated into the vehicle, it will be so seamlessly embedded and covered that the label will not be visible at all.
My shock soon turned into a sense of reassurance.
This was indeed to be expected. Japanese manufacturers are world-famous for being rigorous and dedicated to perfection, across almost all industries, traditional and modern. Naturally, the craftsmanship is demonstrated everywhere in Japan’s automotive world as well.
I once heard a story where a Japanese automaker failed a batch of washers simply because their color seemed slightly different from the original specification. Again, a washer – a thin plate placed under a nut or the head of a bolt, not the one next to the dryer – are hardly visible, and its color does not affect its functionality at all.
So, what does this mean?
You may think: if one focuses too much on trivial details, they may not be able to see wholistically or spend enough time addressing critical issues. This may ring true when it comes to other things, but not for automotive manufacturing.
To me, this is all about process control. The philosophy behind it is very simple – the easiest way to minimize room for error is to establish an absolute standard and procedure for every step. Once you introduce tolerance, you start introducing uncontrollable elements, eventually inviting a whole gang of discrepancies, inconsistencies and inevitably, failures. When “tolerable” small errors add up, products can become malfunctional without any major defect.
Coming from a semiconductor background, I’ve always believed this: if a production yield is 99%, it’s safe to think that the 99 good parts out of the 100 checked are indeed trustworthy; but if a production yield is only 50%, it is very likely that many of the 50 “good” parts are problematic too. In the latter scenario, a low final yield means the process has not been checked and controlled well enough – defective parts should have been identified and eliminated earlier in the process, had there been a proper procedure.
Series lidar productions are such colossal collective efforts that Cepton, starting off as a Silicon Valley innovator, certainly needed guidance on how to establish the right process. Automotive safety is all we talk about at Cepton, and we know the best way to become an OEM-validated and consumer-trusted technology provider is to work with an experienced Tier 1 supplier. I am very grateful that Cepton found Koito.
We needed the rigorous spirit.
In fact, the entire lidar industry needs it. A “quick and dirty” startup mindset is pivotal in driving innovation, but to transform innovation into usable technology, it takes repetitions, redundancy and just an overall obsession with quality and reliability. I see no lidar company, including my own, comparable to a Tier 1 in terms of volume production capabilities and readiness. It might take decades to catch up, so why not collaborate?
Relying on Koito’s extensive knowledge, established manufacturing expertise and reputation for top quality, I feel assured that Cepton has taken the right path in its lidar commercialization to efficiently enable mass-market adoptable and usable solutions.